The term metal (or metallurgical) leaching refers to the processes involved in separating useful metals from non-valuable ore constituents. The science behind these processes, while not a very glamourous topic, is important: beyond the obvious practical necessity of extracting the metals, leaching methods historically have left behind toxic waste products, so modern improvements represent valuable steps towards environmentally friendly resource extraction.
The metals we desire are usually found mixed with other elements and compounds. Methods to extract and purify these metals have been developed over the centuries. Generally, the choice of extraction method depends on the reactivity (tendency to undergo chemical reaction) of the metal being extracted. The following table summarizes extraction methods, with metals grouped by reactivity.
Electrolysis
The leaching methods that are the focus of this article are in the third category, extraction by chemical reaction, but, for completeness, let’s look at examples of the first two methods as well.
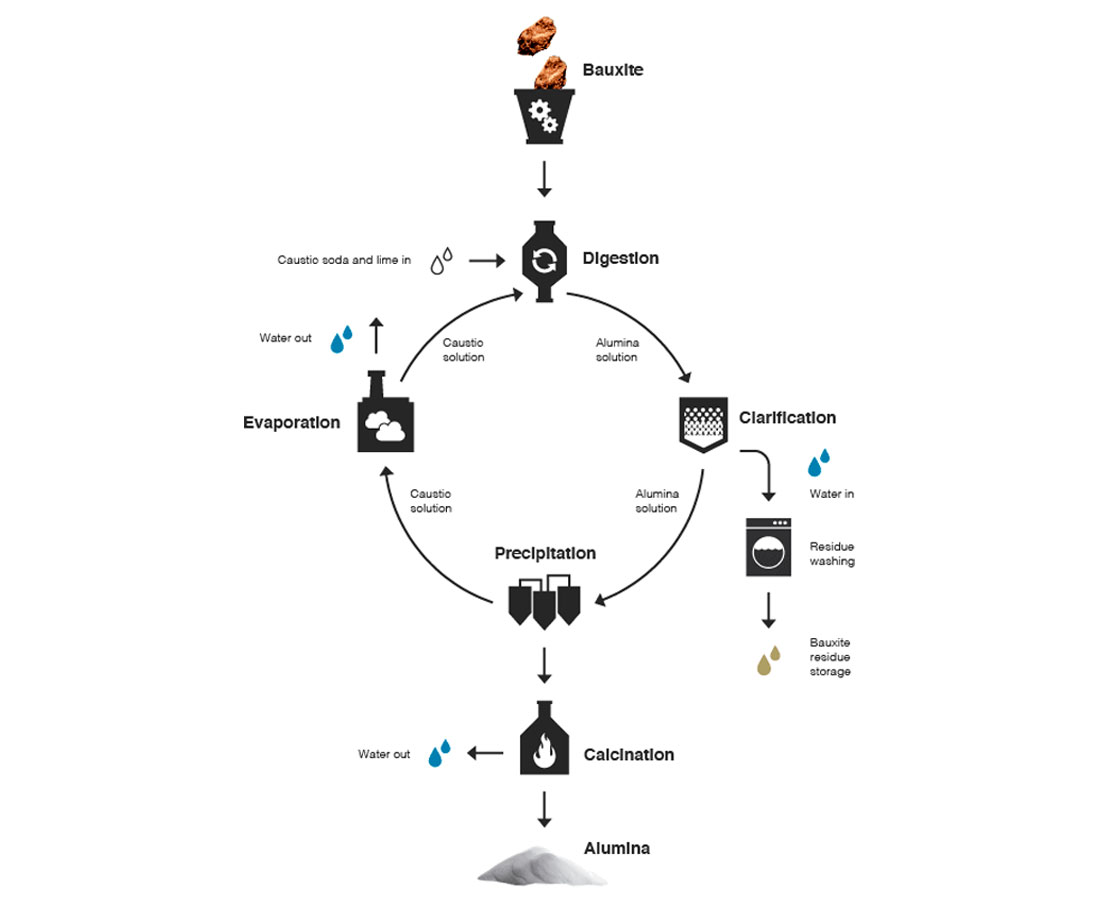
The extraction of aluminum from bauxite ore relies on electrolysis. Bauxite ores typically contain aluminum hydroxide (minerals such as boehmite, diaspore and gibbsite), along with non-aluminum impurities such as iron oxides, quartz and clays. Using the Bayer process (Figure 1) aluminum oxide (Al2O3, also referred to as “alumina”) is produced. The Hall-Héroult electrolysis method (Figure 2) is then used to extract essentially pure (~99.7%) aluminum from the alumina. The alumina is dissolved in molten cryolite (Na3AlF6) to lower the melting point to a more practical ~1000°C. A low voltage (~5V) direct current of 100-300 kA is then passed through the molten liquid. The oxygen binds to the carbon at the anode to produce carbon dioxide, while pure molten aluminum collects at the cathode, where it is syphoned off. The separation is described chemically by Al2O3 + 3/2 C → 2 Al + 3/2 CO2.
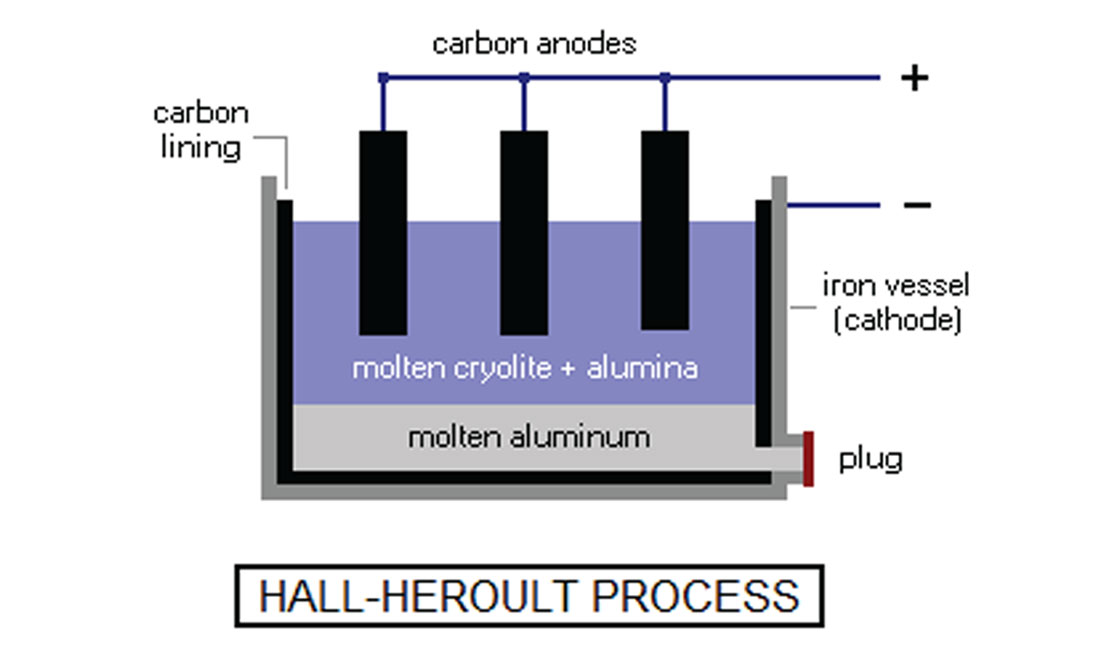
Reaction
To extract iron from an iron ore (common ores include magnetite, hematite, goethite, limonite and siderite) the ore is crushed, powdered, then a reduction reaction with carbon is used. Iron-oxygen bonds are strong, so an even stronger elemental bond with carbon must be presented to the oxygen so that it switches, releasing the iron. It’s a little tricky, because the principal reduction agent is carbon monoxide, not carbon dioxide. Carbon monoxide is produced by combining oxygen and coke (close to pure carbon), then this carbon monoxide is used as the reduction agent in three successive stages, ultimately removing most of the oxygen from the iron oxide ore to produce pure iron. The chemical equations are:
Produce carbon monoxide: 2 C + O2 → 2 CO
First stage: 3 Fe2O3 + CO → 2 Fe3O4 + CO2
Second stage: Fe3O4 + CO → 3 FeO + CO2
Third stage: FeO + CO → Fe + CO2
Calcium carbonate is also used to remove impurities. Iron produced in this way contains about 4% carbon and is too soft to be of much use, so nowadays further steps are taken to produce steel, mainly to remove most of this carbon. More detail on this can be found in the October 2013 Science Break article on steel.
Leaching
Leaching, in the general sense, describes the extraction of a substance from a solid by dissolving the solid in a liquid. When a solvent is added to the solid (made up of an insoluble carrier and the desired solute), the solid separates into a liquid combination of the solvent and solute, and a slurry with carrier solids. The slurry is then removed using physical methods, and the remaining liquid is processed further to extract pure solute.
Metallurgical leaching usually uses an acidic solvent to convert the solid metals into aqueous salts. There are four main categories of metallurgical leaching: dump, heat, tank/vat and in situ.
Dump Leaching
This is a fairly primitive method. Large, uncrushed chunks of ore are piled directly on a leach pad. A cyanide solution is poured over the pile and allowed to percolate slowly through it, dissolving the metal and eventually dripping down onto the leach pad where it is collected. The metal is extracted from the liquid, which is recharged with more cyanide and the process repeated. Dump leaching is relatively cheap, so is commonly used for low grade ores. After a year or two, a typical low grade ore will yield ~50% of its metal in this way.
Dump leaching operations, if not done properly, can result in significant environmental damage. Cyanide can leak from the operation either through an improperly designed or compromised leach pad, or through a settling pond breach or similar operational accident. The abandoned pile, if not properly dealt with, can represent a hazard years after operations have ended. Once in the water table, cyanide obviously poses serious health risks.
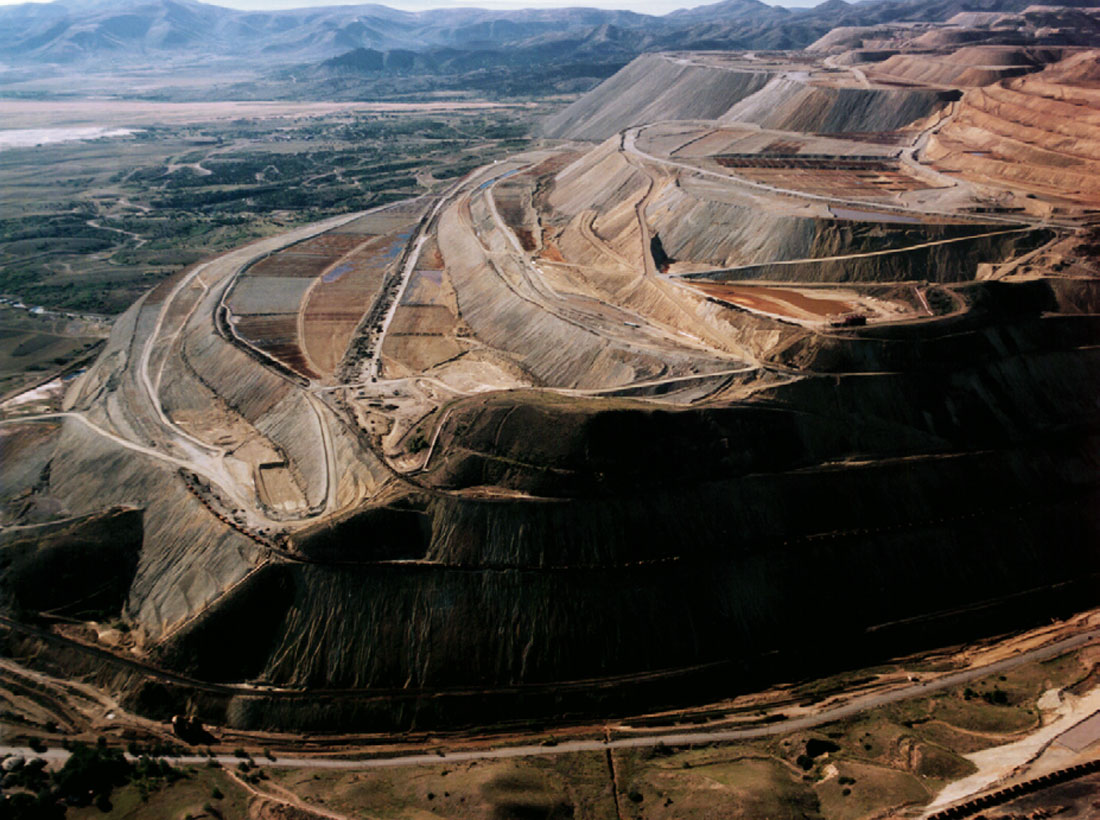
Figure 3 shows the dump leaching operation at Kennecott’s Bingham Canyon mine, a safe and well run mine. It is the world’s largest open pit copper mine, and can often be seen from planes descending to land in Salt Lake City.
Heap Leaching
This method is a progression from dump leaching, with additional crushing, grinding and other optimization steps being done to the ore prior to leaching, in order to improve extraction rates. Figure 4 shows a schematic of the method. The key to optimizing extraction rates is to achieve even permeability throughout the heap; if permeability is uneven, then compact or tight zones will never be exposed to the liquid reagent, thus metals will remain behind, undissolved.
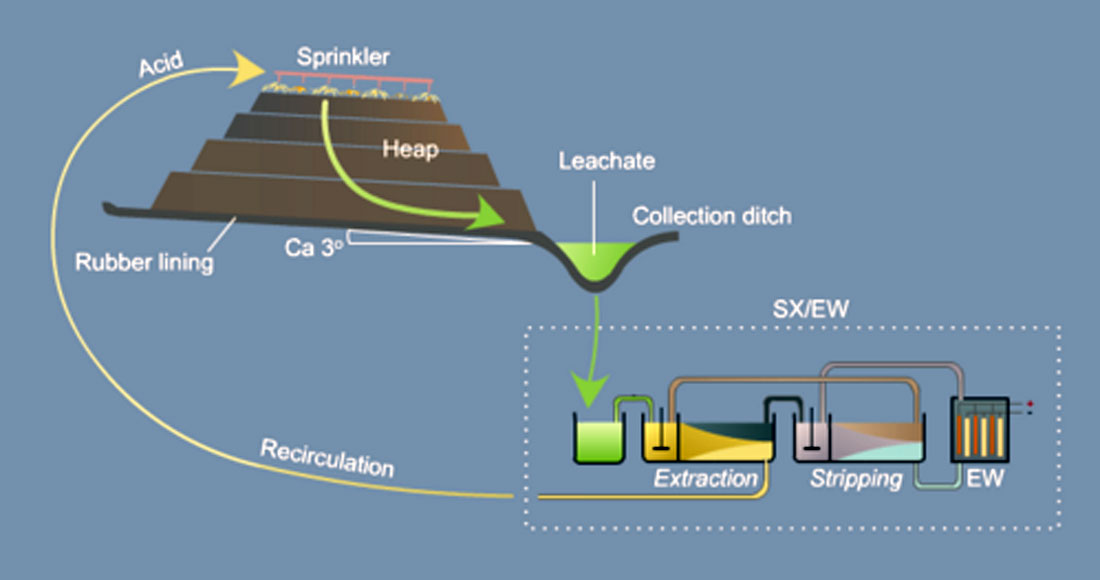
The first step after leaching, solvent extraction, is a liquid-liquid operation designed to purify and concentrate the desired metal ions. The extractant is usually an active hydrophilic group bound to long chain hydrocarbon molecules present in an organic kerosene type diluent. When this fluid is added and vigorously mixed with the metal-rich liquid dripping down from the leach heap, the metal ions bind to the organic extractant. The aqueous phase and the now metal-rich organic phase are allowed to separate, and the latter is stripped and used to create a new concentrated metal-rich aqueous phase. The final stage uses electrowinning to concentrate the pure metal. The last tank in the diagram is an electrolytic cell containing alternating vertical cathodes and anodes; the former are some type of plated metal, usually steel or aluminum, and the latter are made of some kind of inert, oxygen evolving substance like lead dioxide. When the system is charged, the metal is drawn to and collects on the cathodic sheets, while the oxygen evolves on the anodes.
Tank / Vat Leaching
These two methods employ much the same processes as dump and heap leaching, but in a more controlled environment. I’m speculating here, but assume that tank or vat leaching would always be preferable, but the sheer volume of material to be processed with lower grade ores makes that impossible. This would imply that tank and vat leaching is mainly used with higher grade ores. Besides the issue of volume, from a business perspective, higher grade ores would also support the additional capital investment that vat and tank leaching require. Tank and vat leaching are similar. The main differences are that, generally, vat leaching is done in batches while tank leaching is continuous; and with the vat method, the leachate is drawn out at the bottom of the vat and passed on to the next stage, whereas with tanks the slurry from one stage overflows into the next stage’s tank. There can be variations with both methods.
The stages are basically the same as with heap leaching: in Stage 1, the vats or tanks hold a liquid made up of the ground ore and the liquid reagent, Stage 2 holds the leachate, Stage 3 is the solvent extraction, Stage 4 the stripping, and Stage 5 is electrowinning. Because the entire process is so much more controlled, additional things can be done such as fine tuning the density of the slurry, injecting gas (often oxygen), to enhance the processes, agitating the slurry with mechanical agitators to optimize leaching and ion binding, and so on.
In Situ Leaching
Again, this method involves the same basic processes as with dump and heap leaching. Instead of physically transporting the ore out of the mine to be processed, in situ leaching is done right in the mine. The method works with porous, relatively soluble ores. The liquid used is referred to as a “lixiviant”. It is injected into the ore via a borehole, and then percolates through the ore, dissolving it. The slurry like liquid is then collected via a different borehole, and pumped to the surface.
The lixiviant chosen depends on the type of ore and mineral being produced. For potash and various salts, water does the trick. The salars (salt flats) of Argentina and Bolivia contain more than 50% of the world’s known lithium reserves. Battery production is driving a mining boom here. Since the lithium is already held in solution in naturally occurring brines, lithium extraction here is not considered in situ leaching.
Uranium
Almost half of the world’s uranium is produced via in situ leaching. The lixiviant could contain sulfuric acid, nitric acid, carbonate (in the form of ammonium carbonate), dissolved carbon dioxide, or sodium bicarbonate, depending on the ore composition. The uranium-rich liquid is pumped to a plant where it is filtered through resin beads, which attract the uranium through an ion exchange process. The beads are then taken to a plant where the uranium is stripped off the beads to produce “yellowcake”. Yellowcake is the intermediate product shipped by the mines to plants for final processing, refinement and enrichment. It varies from mine to mine, but is mainly made up of uranium oxides, primarily triuranium octoxide (U3O8), with about 20% various impurities. The resin beads, once stripped, are returned to be used again at the ion exchange plant. The extremely high grade uranium ores in Canada’s Athabasca Basin are not processed in situ, but the method is used with most of the rest of the world’s uranium, found in much lower grade ores.
Copper
In situ leaching was probably first invented to extract copper. It was definitely being done in China over 1,000 years ago, perhaps even 2,000 years ago. It is still commonly used today, usually for low grade copper ores. The lixiviant typically contains sulfuric or hydrochloric acid. If the ore has higher sulfide content, then oxidizing agents such as ferric sulfate and oxygen need to be added to the lixiviant. Sometimes bacteria that feed on sulfides, Thiobacillus ferrooxidans, are also used. A hybrid in situ – dump leaching method known as “stope” leaching is also sometimes employed: instead of bringing the ore to the surface, it is moved to a stope that is suitable for the leaching process. Note that stopes are the openings or rooms left behind by excavation; the stepped ones created by mining a dipping vein are perfect for leaching. In this way, the effort of bringing all the ore to the surface is avoided, and the mess can be left behind, underground.
Mercury Amalgamation
I want to end this article with a look at a method that has been used for centuries: mercury amalgamation. Mercury readily forms an amalgam with most metals, notably gold and silver. When clean gold or silver comes into contact with clean mercury, they essentially melt into the mercury to form an amalgam, a grey coloured alloy. These alloys have been used for dental fillings for centuries, but have recently been eclipsed by safer, better materials. Miners over the centuries devised numerous methods for exposing flecks of gold and silver in muds and silts to mercury. For example, during the California Gold Rush, prospectors would put mercury in the riffles (grooves) of their sluice mills. As the gold-bearing mud washed over the mercury, it would be amalgamated into the mercury. The amalgam chunks were then heated and the mercury would evaporate, leaving behind pure gold.
Of course, evaporated mercury gets into the lungs of the miners and their families, and finds its way into the ecosystem. As it works its way through the food chain, it bio-accumulates and converts to methylmercury, an extremely dangerous neurotoxin (e.g. search on Grassy Narrows and Minamata disease). An interesting side note is that the term “mad as a hatter” derives from the fact that 18th Century hatters used mercuric nitrate to form felt from animal hairs, and the daily exposure to mercury vapour often caused insanity in the long run.
I have read horrific accounts of the Spanish silver mining operations in Potosí, Bolivia in the 1500s. Enslaved natives were used to operate an amalgamation process known as the patio method. Crushed silver ore was mixed with salt, water, magistral (a form of copper sulfate) and mercury, and spread out into an approximately 60 centimeter thick layer in a low walled patio. The slaves would then stomp around in this mix for a few weeks until a silver-mercury amalgam formed. It was then melted and separated. The slaves usually died within a few months, and were replaced.
Nowadays, professional mining companies use the other leaching methods I have described, as they are more effective and much safer. However, a good deal of unprofessional mining referred to as “artisanal” is still conducted in numerous underdeveloped and under-regulated countries, and these types of operations continue to damage people and the environment. The UN estimates more than ¼ of the world’s gold production is from artisanal mining, and that 95% of the mercury they use in a year, approximately 1,000 tons, is released into the environment. I should note as well that many small scale mines are operated very safely and professionally – small scale does not necessarily mean irresponsible.
Conclusion
The mining industry is continually developing new and better ways to extract metals from ores. For example, I just read an article featuring several exciting new gold extraction methods (Chadwick, 2016), and also recently, Barrick announced that it has developed a method which uses brackish water, not fresh, and does not require cyanide or lime, to extract copper and gold from ores. These are examples of the type of improvements being pursued that are continually making leaching and other aspects of mining safer. Increased environmental awareness has raised the level of scrutiny and number of regulations imposed on mining companies, so the type of accidents that were commonplace historically have been greatly reduced. However, as long as some miners employ dangerous leaching methods, the environment will continue to suffer.
Share This Column