Introduction
The introduction of new, light weight, cable-free seismic systems may inadvertently be increasing the risk of litigation liability for users of existing cable-based seismic systems. The latest cable-free systems offer considerable advantages in terms of Health and Safety, as well as reduced environmental impact, and may, by virtue of their very existence, present some serious challenges to the seismic operations “status quo”. Now that one of these systems in particular has demonstrated its legitimacy on a number of “real” land operations, the challenges should no longer go ignored.
Background
In 2001, Ascend Geo LLC was formed as a wholly-owned subsidiary of Aspect Energy, a major independent oil company, to develop and ultimately deliver a performance optimized, cost-effective land/TZ seismic recording system. Ascend’s objective was to deliver significant acquisition savings to the parent company, which had been experiencing significant 2D and 3D survey cost increases using other state-of-the-art hardware. Once the system was developed and field tested, Ascend Geo began the process of commercializing the “Ultra Seismic Recording System” and packaging it for sale both domestically (US) and abroad.
Any new acquisition technology claims to bring advantages and this was the case with Ultra. Being a “remote recording” system, it offers far lower weight, reduced environmental impact and improved productivity. A barrier to adoption of this technology has been that, despite increasing worldwide approval of blind shooting, some segments of the broader industry have not yet completely accepted the technique. It is, however, difficult to deny that if this industry wants to see more crews, as well as larger ones, we cannot go on the way we have been; not even with oil at $60/bbl. Although many in Canada are still sympathetic to the sentiments that exist against the notion of shooting blind, the more we consider the issues the more we are convinced that cable-free systems are a legitimate answer (perhaps the only legitimate answer) to some specific needs within the industry, especially those related to Occupational Health & Safety.
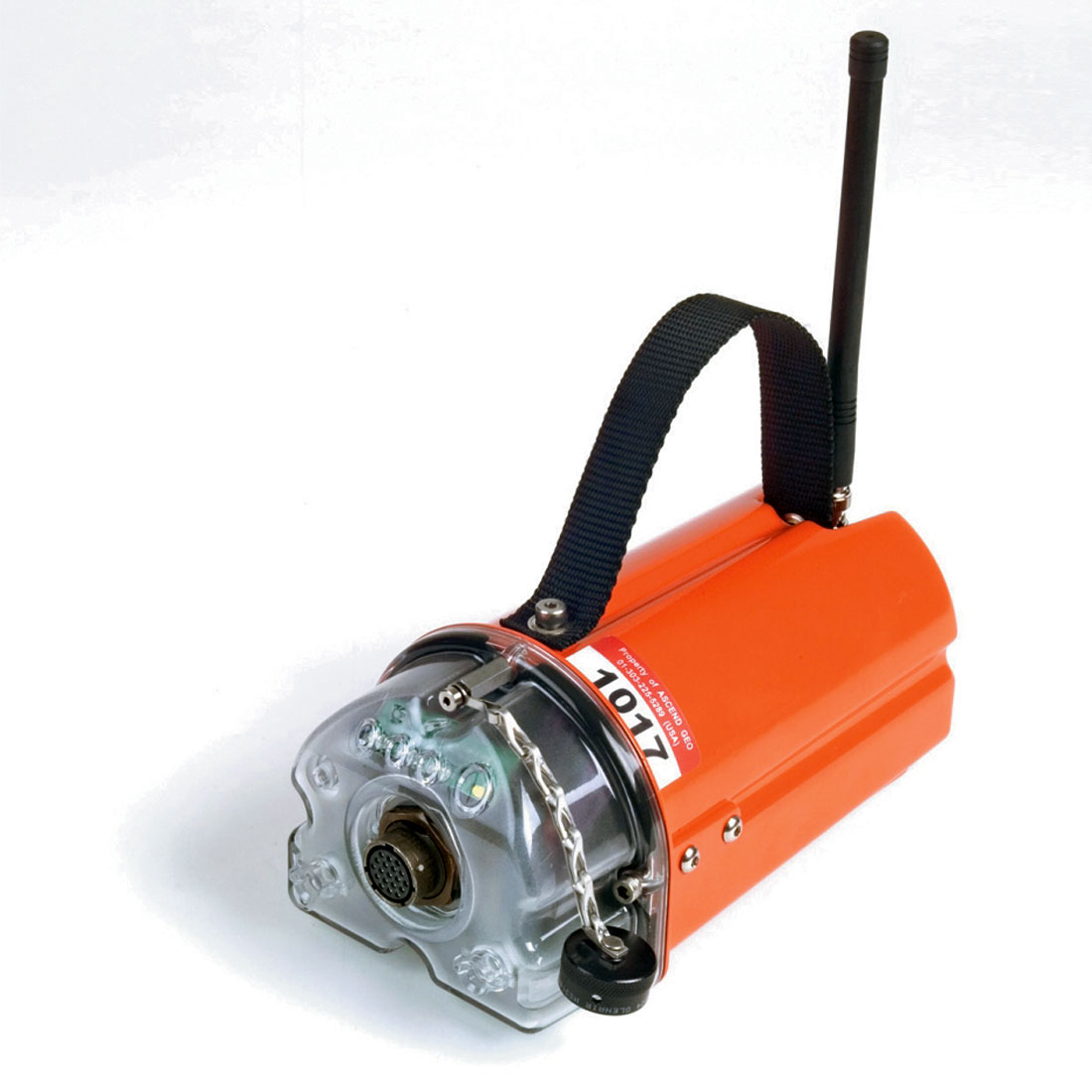
We were attempting to answer Gijs Vermeer’s call for a weight comparison between the newer cable-free systems and existing cable-based technology (difficult to state, unequivocally, due to variations in sensor weight – a not insignificant factor in calculating overall system weight) and it struck us that, while total system weight was significantly reduced, the individual component weights may be dramatically lower without the long lengths of telemetry cable to worry about.
Our examination of the Ultra system awoke a conditioned response, learned as a General Manager of a contracting firm in Ottawa (Canada’s political and litigation capital). That response might be characterized as “litigation liability awareness” and, in anybody who’s been exposed for any length of time to the voracious appetites of Ottawa lawyers, it elicits powerful avoidance behaviors. When we considered the unbelievably low weight of the Ultra system, around 1.5 - 2 lbs / channel (including battery for around 100 hours) and how that may benefit worker safety, we became somewhat concerned about how its existence might affect current land seismic operations.
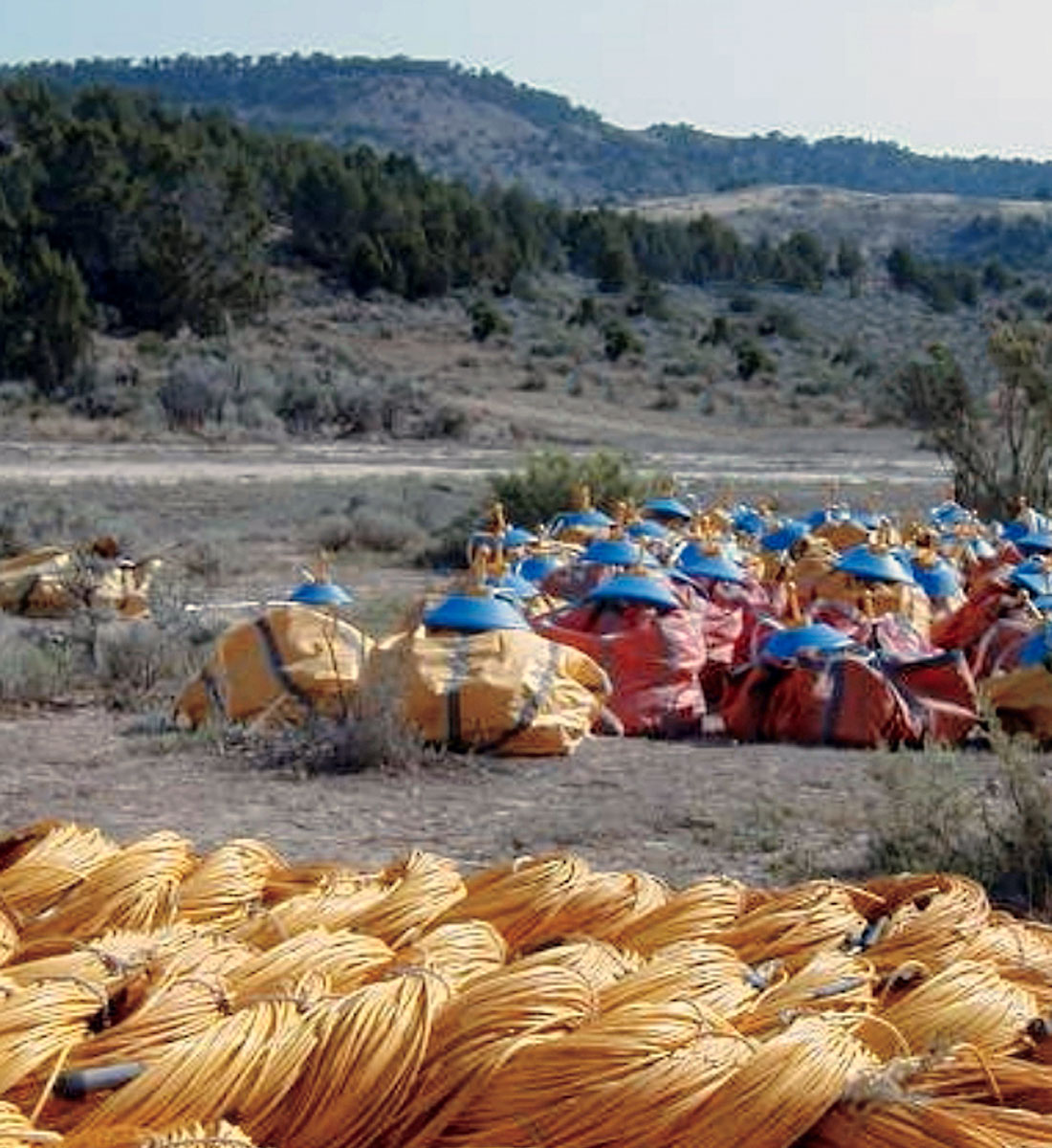
Cable-free systems are not new to land seismic. One thinks of SGR a few decades ago and Input Output’s RSRmore recently. Ultra, however, is one of the new generation of cable-free system and what is especially important, at the time of writing, is that Ultra alone seems to have been used in a variety of real field conditions. Therefore, it does not suffer the stigma of vaporware or theory which attaches to some new hardware well after launch (and before real use) and so one must now start to take more seriously Ultra’s possible impact.
It occurred to us that the new generation of cable-free systems now advertised may be bringing with them an Occupational Health & Safety “storm cloud” for seismic data acquisition companies and, potentially, the oil companies who contract them.
Manual Materials Handling – a Primer
Historically, every improvement in system size and weight has been heralded as a boon to Health and Safety but very few of us understand the exact mechanisms by which weight affects safety so we have become accustomed to nodding our heads and agreeing, vaguely, that some safety improvement must attend weight reduction.
In Alberta, the Occupational Health and Safety Act (“AOHS”) is administered by the Minister of Human Resources and Employment and the ministry offers a number of publications dealing with the risk of workplace injury, including:
“Lifting and Handling Loads – Part 2 Assessing Ergonomic Hazards”
URL: http://www.hre.gov.ab.ca/documents/WHS/WHS_PUB_bcl002.pdf.
This AOHS document offers a lifting assessment tool which may well have been used to develop the seismic industry’s de facto standard lift load of 40 lbs, a limit often attributed to a major international (European) oil company. As one might expect, the European Union has similar documents, in 17- languages, which affect any crews working within its extensive reach.
The AOHS document provides the attached diagram (Figure 3 – AOHS Lifting Tool), taken from a similar State of Washington Department of Industry and Labor (“WDIL”) publication, to establish maximum lifting weights for load positions relative to the worker’s centre line. These weights are reduced based on frequency of lift and asymmetry (twisting) performed during the lift. Given a seismic load’s location (+/- 10” from the body at ground level) and a reduction of 0.85 for frequency of operation, it might be reasonable to conclude that the maximum safe load weight should be no more than approximately 40 lbs.
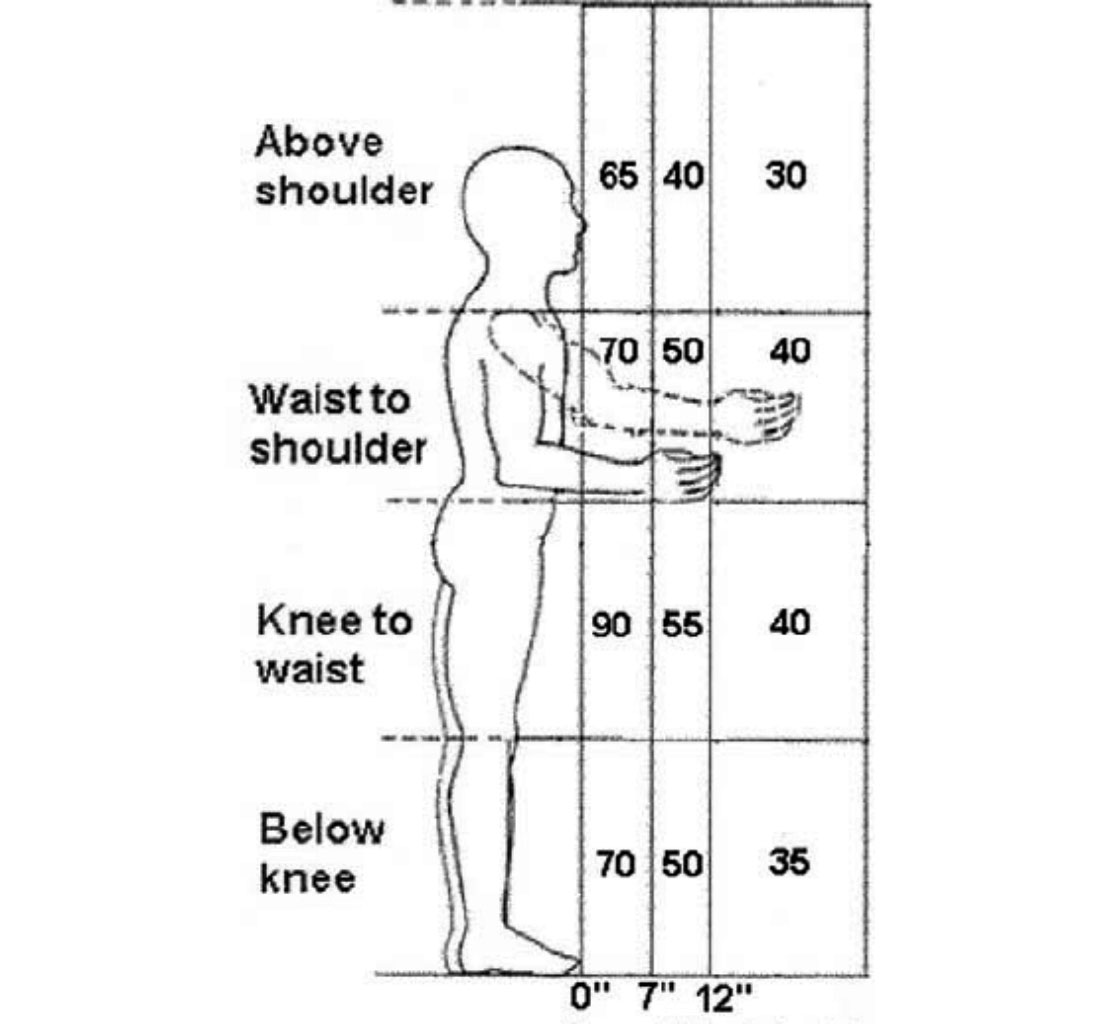
There are, however, significant problems with that conclusion. The AOHS document, and the WDIL document upon which it is based, refers to the US National Institute for Occupational Safety and Health (“NIOSH”) “Revised Lifting Equation” as the source of their lifting evaluation tool.
NIOSH is one of the world’s leading authorities on workplace safety issues and in 1993 NIOSH published a guide for employers to develop a better understanding of safe weight load limits for workers and a methodology for calculating a Recommended Weight Limit (“RWL”) for lifting tasks, known as the revised lifting equation.
The RWL is used to derive a “Lifting Index” (“LI” = Actual Load Weight / RWL). The Lifting Index provides a measure of the risk to employee health associated with various lifting tasks. A task with a Lifting Index of 1.0 is considered to be one which any healthy worker could perform without increased risk of injury. From NIOSH:
“… it is likely that lifting tasks with an LI > 1.0 pose an increased risk for lifting-related low back pain for some fraction of the workforce (Waters et al. 1993). Hence the goal should be to design all lifting jobs to achieve a LI of 1.0 or less.”
The WDIL and, by default, the AOHS felt that setting the limit at 1.0 would be too difficult for many employers to achieve and, therefore, the NIOSH lifting equation was compromised. From the (122-page) “Concise Explanatory Statement” of the WDIL:
“The final rule has been modified to approximate Lifting Equation levels of approximately 1.5 - 1.7 at extended reach lifts and 2.0 at the least stressful near reach lifts. The department chose this as the best balance among safety, feasibility and simplicity.”
To see exactly how much of a compromise has been made from the original revised lifting equation we may reference NIOSH directly:
The Recommended Weight Limit (RWL) is defined as follows: RWL = LC x HM x VM x DM x AM x FM x CM
Where:
LC = | “Load Constant” (23 Kg or 51 lbs) |
HM = | “Horizontal Multiplier” (distance between gravity centres of the load and worker) |
VM = | “Vertical Multiplier” (derived from the height of the load at its origin) |
DM = | “Distance Multiplier” (from the height the load must be lifted or lowered) |
AM = | “Asymmetric Multiplier” (derived from the off-centre nature of the load, if any) |
FM = | “Frequency Multiplier” (number of lifts over time, or the recovery time available) |
CM = | “Coupling Multiplier” (derived from the ease with which the load may be handled) |
Note that NIOSH’s Load Constant, of 51 lbs represents the heaviest possible load (under ideal lifting conditions) that will result in a Lifting Index of 1.0 or less and, therefore, not increase the risk of injury to an average worker in good health.
HM: For Seismic loads the distance between the load’s centreline and that of the worker is less than 10” so the Horizontal Multiplier can be set to 1.0.
VM: The height of the load (or the point at which the load is grasped, i.e. the handle), at the origin of the lift, is somewhere between 0” and 6”; settling on 5” and utilizing the charts provided by NIOSH yields a Vertical Multiplier of 0.81.
DM: The distance that the load must be lifted is from an origin of 5” to the extent of the worker’s arm (30”) or 25” of lift. NIOSH provides a table which yields a Distance Multiplier of 0.89.
AM: The Asymmetric Multiplier is difficult to assess, for seismic loads, since the load is usually either perfectly balanced (a battery pack in either hand) or completely imbalanced (a battery pack in one hand). Assume a balanced load (for reasons stipulated below) and AM = 1.0.
FM: The Frequency Multiplier for seismic workers is based on the duration of the task (up to and including 8-hrs a day) and the average frequency of lifting. Using the same frequency stipulated on the AOHS example yields an FM of 0.85.
CM: Seismic equipment has been designed, with years of experience, to be as easily handled and managed as possible (with the possible exception of cables which, by their nature, cannot always be packaged or utilized with predictable ergonomics); so a Coupling Multiplier of 1.0 may be used.
The RWL begins at 51 lbs and is reduced, based on the actual load and lift conditions, by each of the multipliers to RWL = 51 lbs x 1.0 x 0.81 x 0.89 x 1.0 x 0.85 x 1.0.
The result of the NIOSH equation is surprising; rather than the 40 lb safe workload limit used as the de facto standard for the seismic industry for at least the last decade, NIOSH’s equation would indicate a Recommended Weigh Limit of 31.25 lbs, a 25% reduction from the current standard.
Far more important, however, is the fact that the NIOSH guidelines are constrained by the following factors:
- Applicable only to two-handed lifts (one handed lifts, which are common with seismic loads, are more stressful on the musculoskeletal structure).
- Applicable only to workers on smooth floors with adequate traction (rough terrain or loss of traction due to rain or ice is more stressful on the musculoskeletal structure).
- Applicable only to workers in controlled environments between 19C (66F) and 26C (79F) at 35% to 50% relative humidity (cold or hot temperatures can significantly affect joint and muscle flexibility and fatigue).
- Applicable only to workers who lift and lower loads from a standing position; risk of injury may increase significantly if loads are carried.
All of these conditions significantly and adversely affect the risk of musculoskeletal stress during lifting, all of them exist in seismic field work, and all of them invalidate the 31.25 lbs load design limit set forth by the lifting equation. Suffice it to say that, in the absence of an in-depth study of the ergonomics of specific seismic loads under specific field conditions, targeting load weights significantly lower than 31 lbs might be considered a necessity in mitigating the risk of injury to seismic workers. Again, in the absence of studies, one might be thinking of load limits in the 20 – 25 lb range.
Anatomy of a Problem
It goes without saying that reducing load weights as suggested above would be operationally difficult and potentially expensive. We’ve been using 40 lbs as a weight limit for a number of years and if there haven’t been any significant issues with that then, surely, this isn’t a problem that requires addressing. This begs the question, is there a problem with the 40-lbs limit?
To answer that, we looked to the Workman’s Compensation Board of Alberta for injury statistics and, it seams, there is evidence to suggest a problem.
Alberta’s Seismic workers report an astonishing two times greater incidence of traumatic strain and sprain injuries, as a percentage of all lost time injuries, compared to the Alberta worker population as a whole; 67% of all lost time injuries in seismic, as compared to 33% for the broader population. More alarming, injuries to the back and lower extremities occur nearly three times more often among seismic workers than the average for all workers in Alberta.
Clearly, then, there is a problem. Our existing assumptions about either the 40 lb “safe” weight limit or the average weight load of our seismic workers is not consistent with safe work practices elsewhere across the province. There appears to be a significantly increased risk of injury associated with the way our seismic labor undertakes manual materials handling.
A Problem Translates to a Liability
Why is this situation a problem for employers? The answer, in a word, is “negligence”. In many jurisdictions, including Alberta, employers have enjoyed protection from liability, in cases of worker injury, by the existence of no-fault workers compensation legislation (in Alberta, the WCB Act). Recently, however, many of those same jurisdictions, including Alberta, have allowed cases to be heard where employee injuries have arisen as a result of an employer’s negligence.
Negligence arises from three conditions: 1) the existence of a duty of care, 2) a breach of that duty and 3) damage arising as a consequence of that breach.
With respect to condition 1) the existence of a duty of care, this duty is widely recognized both under common law and as stipulated by workplace legislation. In Alberta the Occupational Health and Safety Act states that “OHS 2.(1) Every employer shall ensure, as far as it is reasonably practicable for the employer to do so,(a) the health and safety of (i) workers engaged in the work of that employer...”
With respect to condition 2) a breach of that duty, how can continuing to perform work as has been standard practice for decades be deemed a breach of a duty of care?
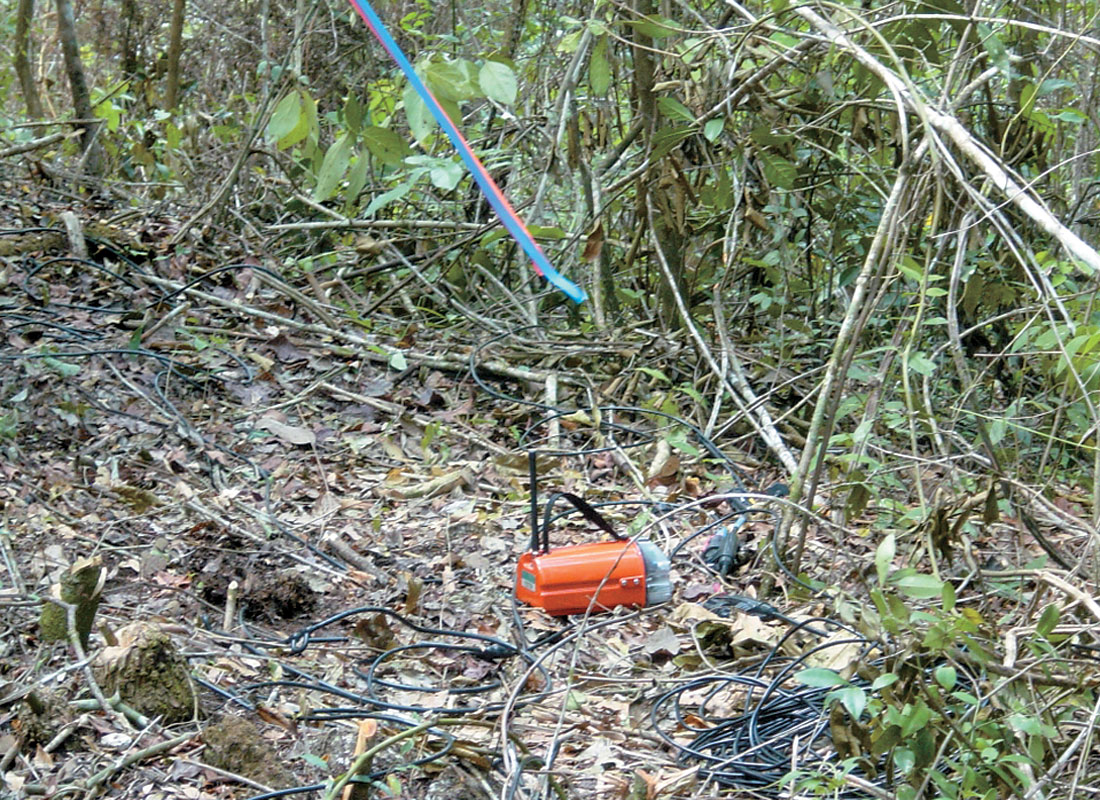
There are two factors that affect breach. The first is foreseeability. Is it foreseeable that carrying loads of up to 40-lbs under adverse (field) conditions may result in traumatic injury? The answer, based on advice from experts (NIOSH) and statistics available is yes.
The second factor is due diligence. Has an employer done everything reasonable to mitigate the risk of injury? The answer lies within the OHS (or similar) acts. So long as the work was consistent with standard practice, the loads were as small as was practically possible, and all other precautions had been taken, then the rate of injury may simply have been considered an unavoidable risk factor for seismic workers and this, historically, has been the case.
Bear in mind that, as a principle of liability law, it is far more important that an employer take every reasonable precaution towards eliminating the risk of injury than it is to successfully eliminate the injury. If our current approach were the only practicable one, given the equipment and resources available, then it may be deemed an intrinsic risk inherent with seismic work and not a breach of duty. No liability would accrue to the employer or contractor. If, on the other hand, a practical alternative did exist, then the failure of an employer to adopt new, safer work practices may be deemed as a breach of their duty of care.
As to condition 3) harm arising from that breach… if historical injury statistics remain valid, looking forward, an injury will likely occur, sometime in the next five to seven days, which may be construed to have arisen from such a breach; the proximate cause of the injury being a requirement to carry an over-heavy load under non-ideal conditions.
Looking forward to Change
Each new generation of seismic equipment has promised, and for the most part delivered, improved field management and increased system reliability. But while equipment owners tend to adopt new equipment primarily on the technical merits (digital telemetry vs. analog; 24-bit vs. IFP) use of new generation cable-free systems can reap a secondary benefit since the use of much lighter equipment may be deemed a responsible and conscientious act to mitigate the risk of worker injury (as is responsibility of every employer to do) .
Not only does lower weight provide immediate benefits, according to Ian Jack… “the benefits of the lighter equipment were clear and tended to be better than predicted, as reduced effort in deployment and retrieval activity (manpower, vehicles, helicopters) tended to have a further positive de-escalating effect e.g. in support services and also in HSE risk.” The “addiction” to cable-based systems will, however, always limit other benefits which are available by switching to cable-free.
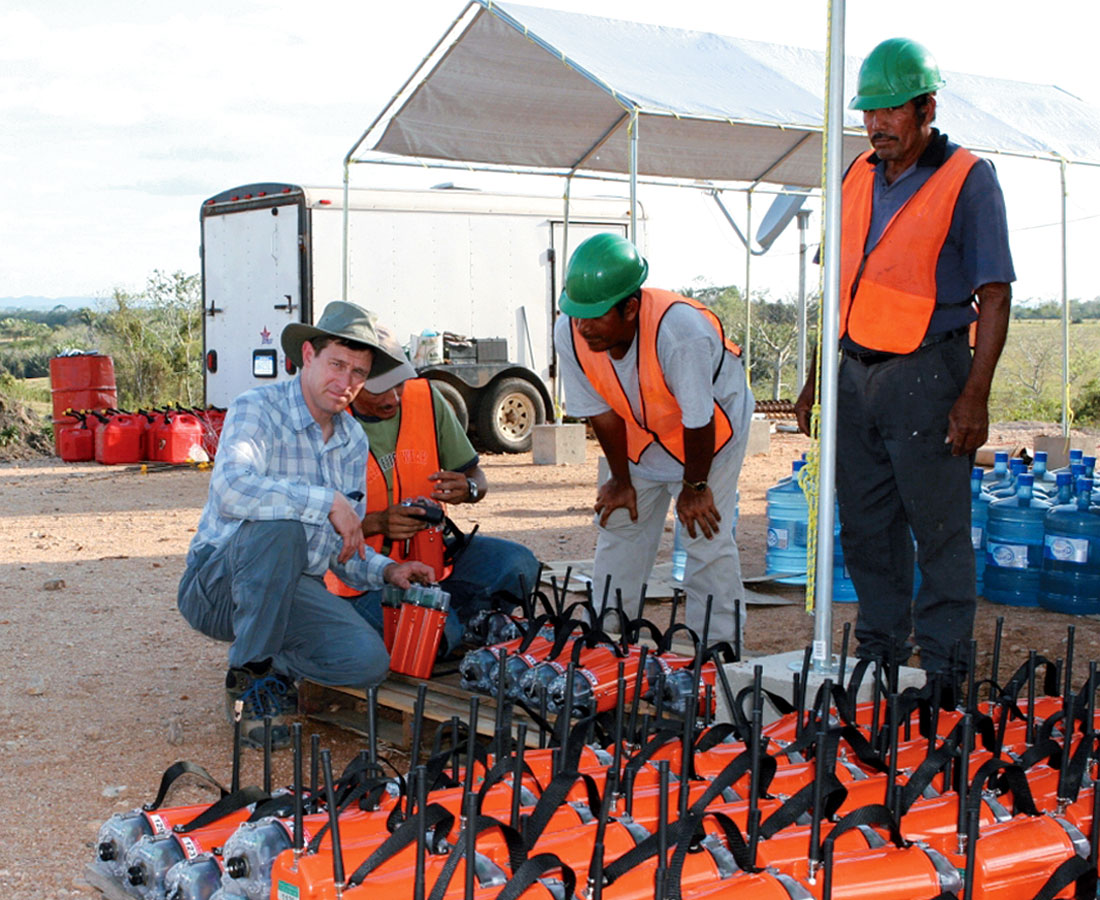
It would appear that cable-free systems such as Ultra represent a practical alternative. Some comparisons would indicate that a 1,000 channel cable-free system could weigh as little as 25% (for a point receiver arrangement) – 50% (were we to keep our geophone arrays as advised by Heath and Cooper) of an equivalent 1,000 channel cable-based system. It is, however, the weight of the individual components of that system which lend it superior HSE performance. A fully powered (100 hour) 3-channel Ultra DAU, weighing in at only 5 – 6 lbs, provides a clear advantage over 3- channels of single station units plus 150-meters of cable at 31 lbs or any breakdown of equipment for multi-channel systems.
Today it seems, thanks to the introduction of new cable-free systems, the employer’s duty of care has become somewhat more exigent as these systems clearly do represent a practicable alternative to today’s heavier cable-based telemetry systems, which may have contributed to a high rate of injury, and may foreseeably continue to do so. Despite whatever warts the end-user might attach to these systems it is inevitable that they will have a significant impact on the way we conduct seismic surveys. And, since forecasts indicate that over 50% of channels sold by 2010 will be cable-free – a timescale during which most systems now being purchased will still be still be on-the-books – it would be a mistake to ignore them.
That is not to say that cable-free systems offer the only solution to these problems. Sharing the weight among additional personal would be one alternative, though we suspect not very popular. But in order to be perceived as undertaking practicable steps to mitigate health risks, seismic companies and contractors may need to pressure existing cable-based manufacturers to rethink the packaging of current systems.
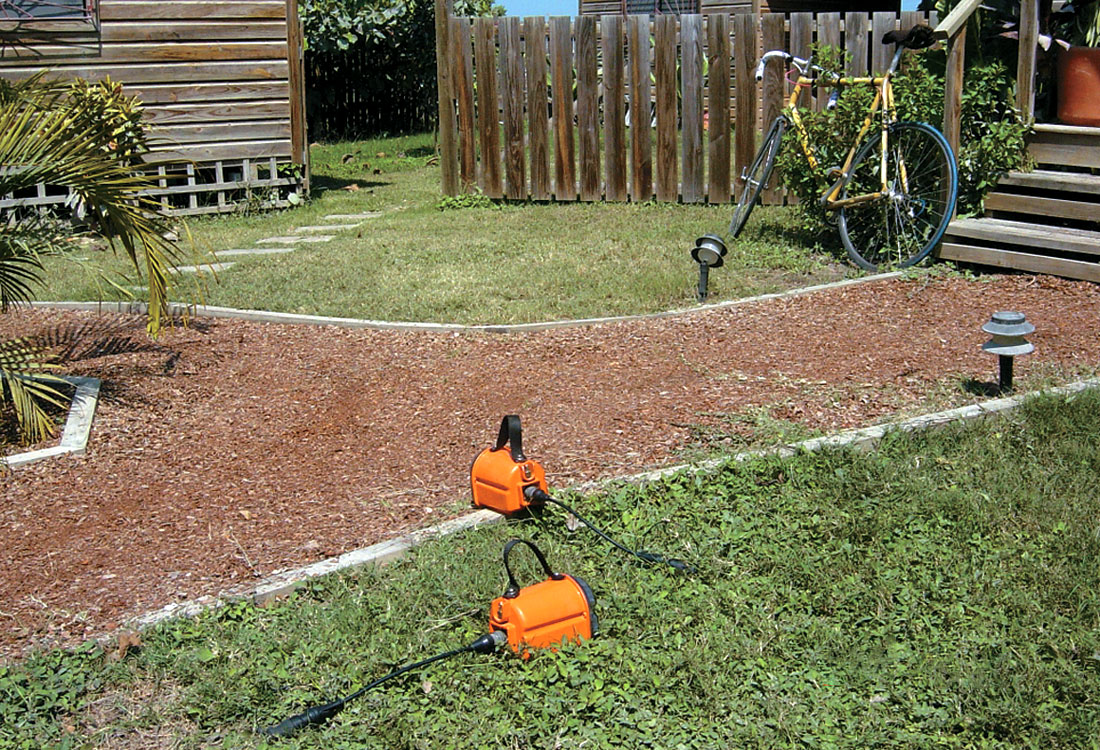
Telemetry cables may need to be segmented into shorter, lighter lengths, despite the attendant downside of doubling or more the number of connections that must be made and maintained. Acquisition units may need to be packaged with fewer channels, again, despite other practical concerns. Battery modules may, perhaps, be reduced and deployed with greater decentralization. Unfortunately, all of these possible solutions exact a price in terms of logistics and/ or reliability.
Alternatively, contractors could look to hiring practices as a method for mitigating risk of lifting injuries. An excerpt from NIOSH advises that:
“… worker selection criteria may be used to identify workers who can perform potentially stressful lifting tasks (i.e., lifting tasks that would exceed an LI of 1.0) without significantly increasing their risk of work-related injury”
In today’s labor market, however, there is little doubt that this methodology would further thin an already over-taxed labor pool.
Summary
Although this article has concentrated on the legal and other HSE - related benefits of cablefree systems in the Canadian market, in this magazine we should not ignore the geophysical advantages. The reality of 24-bit seismic systems is that their main benefit is not some arbitrary level of dynamic range or harmonic distortion versus IFP system – there is little to choose from between them. What 24-bit systems should have let us do is vastly increase crew channel counts over IFP technology. Whether used for point array acquisition, better offset and azimuth sampling or multicomponent recording, vast increases in channel counts are required. 24-bit systems provided technology which was low enough in power requirement and high enough in reliability to make this a possibility, but the adherence to cable-based systems has effectively choked our ability to logistically (or financially) develop mega-channel operations . Cablefree systems will more effectively unleash the advantages of 24-bit and we will, finally, stand a chance of realizing the improvements in seismic imaging we have all talked about.
Join the Conversation
Interested in starting, or contributing to a conversation about an article or issue of the RECORDER? Join our CSEG LinkedIn Group.
Share This Article