In last month’s article, I pointed out similarities between seismic processing and sewage treatment. Since then, CSEG member and seismic R&D programmer Alex Falkovskiy emailed to say that the articles on encryption (March & June, 2013), got him thinking about how data decryption and seismic processing are the same – both involve inverse problems. Interesting – he’d know. But this month’s topic, steel, is in no way similar to seismic processing. Except perhaps that at current prices, seismic processing is a steal... (sorry).
Steel has become such a widely used material that we take it for granted. Approximately 1.3 billion tons of steel is produced annually, in a broad range of forms, to be used for an even broader range of purposes. To do the topic justice would require far more space than is available here, as the production of steel touches on several complex topics, including chemistry, mineralogy, metallurgy, smelting and materials science. Instead, we’ll just skim the surface of three main areas – steel’s composition, history, and modern production.
Composition
Steel is an alloyed metal made primarily of iron (Fe), with carbon (C) being the main alloying element, making up between 0.002% and 2.1% by steel’s weight. Adding carbon prevents dislocations and associated voids (Figure 1) within the iron’s crystal lattice structure, and so steel is harder and stronger than iron, at a price of increasing brittleness and lower ductility. If the amount of carbon present exceeds 2.1% then the alloy is called cast iron, not steel, and its defining characteristic is that it is not malleable, even when hot.
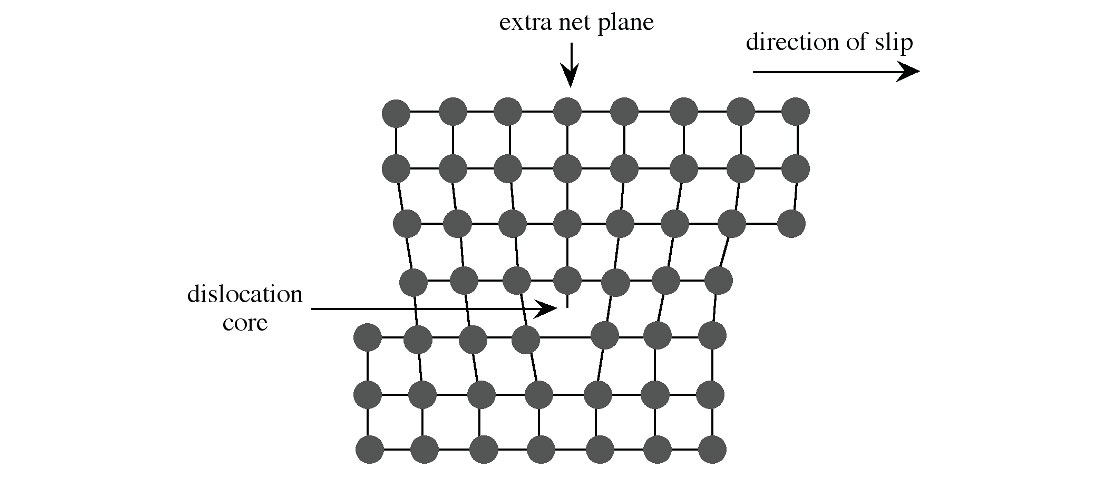
Several other metals are used as secondary alloying agents to achieve other desired properties within the steel besides hardness.
When iron and carbon are combined, heated and cooled, several phases of materials can be formed within a fairly narrow thermodynamic window as shown in Figure 2.
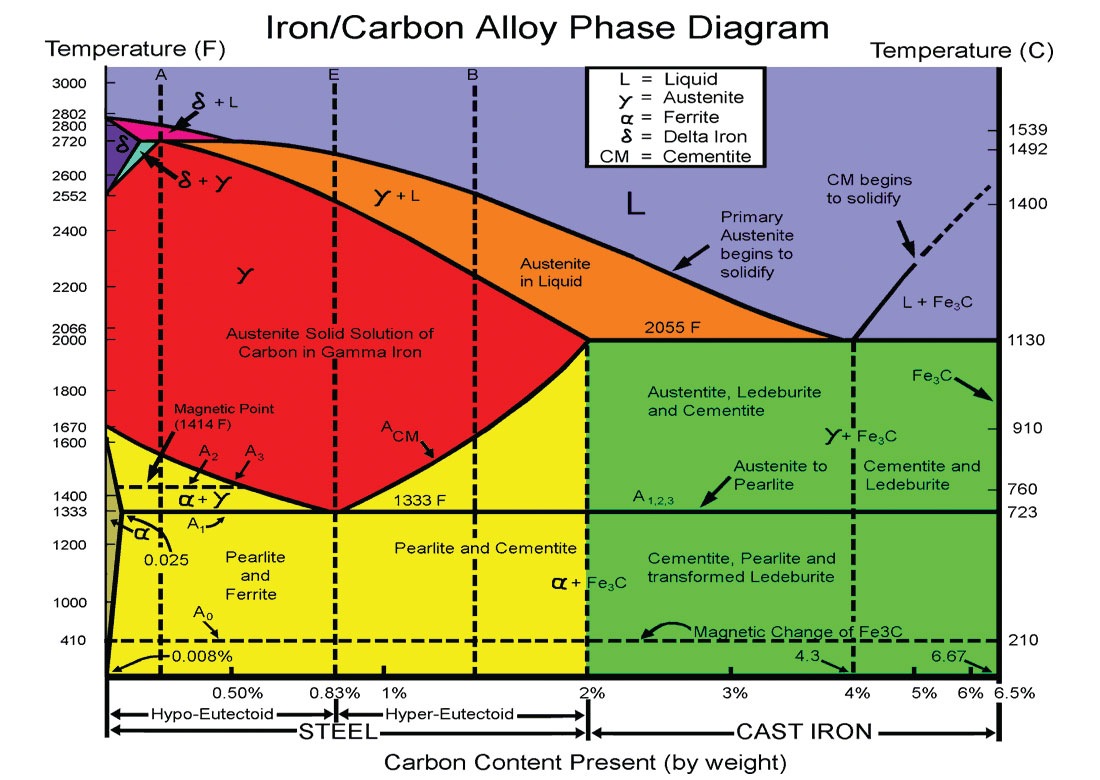
The Fe-C phase diagram is complicated, but it describes what type of microstructures will form within the steel as it cools (moving from the red zone into the yellow), depending on the percentage carbon and the rate of cooling, basically falling either within the left hand side of the yellow region (hypo-eutectoid) or the right hand side (hyper-eutectoid). Cementite is harder and more brittle than ferrite, therefore hardness goes up with higher carbon content and ductability goes down; fine pearlite is harder and stronger than coarse pearlite, the former occurring with rapid cooling, the latter with slower cooling. In a very crude sense this shows how controlling the rate of cooling and percentage of carbon gives the desired physical properties of the steel produced, and then of course this is further modified with the introduction of the secondary alloys as summarised above.
Heat quenching, that is speeding up the cooling of the steel, for example by submerging it in water, can make the steel harder, as if done properly it prevents the separation into phases and microstructures as discussed above. Heat quenching is usually followed by tempering – a reheating of the steel to a lower temperature – to reduce the brittleness caused by the quenching. The entire field is extremely complex and difficult to grasp, so we’ll leave it at that. To be honest, the phase diagram stuff brings back horrific memories of an igneous petrology course I took in university (I’m still scarred by the experience), and I’m more than happy to move on to the history of steel.
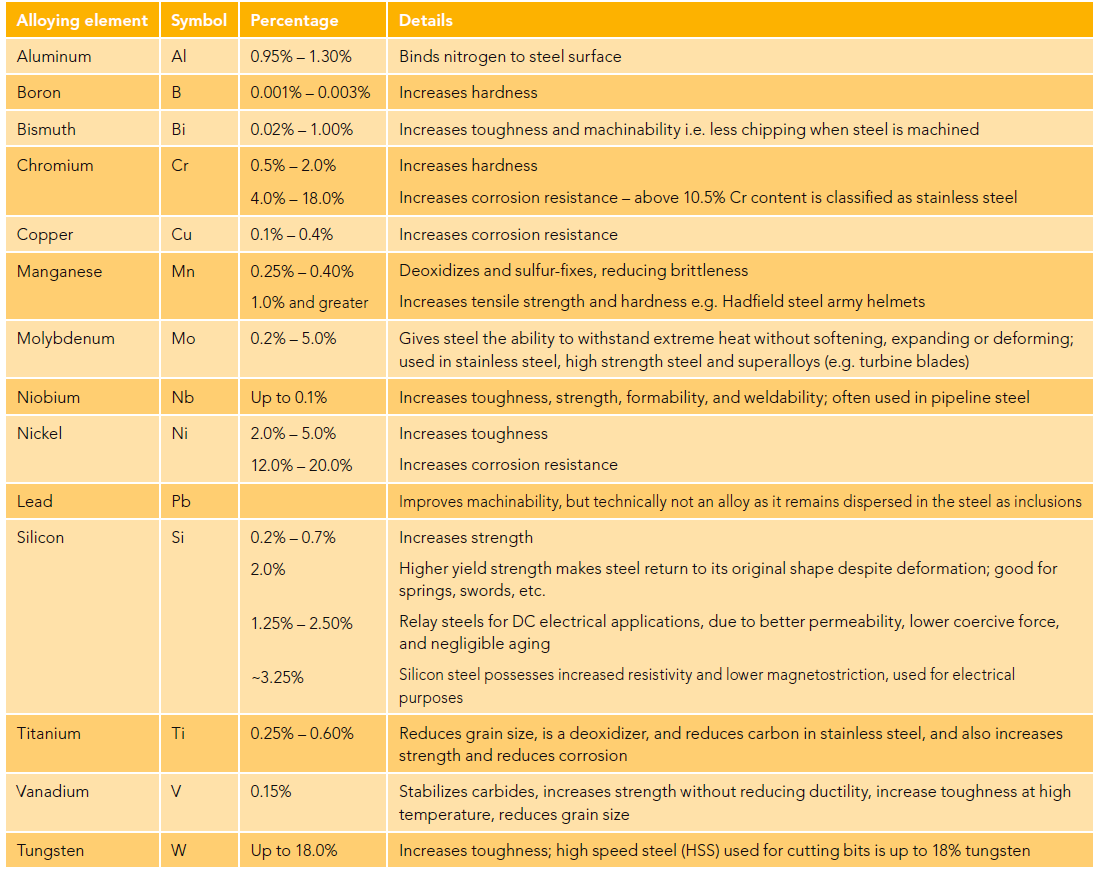
History
Considering iron’s melting point is an extremely high 1,528 °C, the history of steel making goes remarkably far back in time. Prior to that, humans had of course been working with several metals with lower melting points, starting with copper in about 7,000 BC. Copper is soft, melts at 1,083 °C, is easily worked and is found in its native form in many places. By about 4,000 BC humans were mining and smelting copper. Around 2,800 BC the process to create the alloy bronze was developed – the combination of copper and tin creates a metal that is harder than either of its constituents, and it can take a sharper edge. This technology was invented in Sumeria, and then quickly spread to Anatolia and east to India and eventually China.
There is evidence of experimentation and early efforts at producing iron almost 4,000 years ago, but these just produced beads, rings, primitive blades and the like, and archaeological evidence suggests the Iron Age proper didn’t start until around 1,500 BC, with Hittites producing relatively large volumes of iron products. The crude smelting technology used to make bronze with temperatures of ~1,300 °C had difficulty melting iron, and would have produced messy clumps of softened iron mixed with slag and impurities, especially carbon from the charcoal used – this is known as bloom or sponge iron. It then had to be hammered and worked (i.e. wrought) to physically remove the impurities, resulting in a carbon content of about 0.02% to 0.08%, lower than steel. Early wrought iron products would actually not have been as hard as bronze, but must have held some sort of appeal, perhaps as a new technology, or because of different or superior workability.
There is no consensus on when steel was first produced, but it likely was created sporadically, perhaps by accident, throughout the Iron Age. Fragments of steel have been dated to ~1,800 BC in a site known as Kaman-Kalehöyük, located about 100km SE of Ankara, Turkey. There is a disputed date of 1,500 BC in East Africa, and similar hints of ancient steel making elsewhere on that continent. In the 11th century BC metal workers in the Middle East discovered that by reheating iron in a furnace with charcoal, the metal absorbed carbon and became much harder, while still retaining some of the malleability of iron. It was at this time that steel first began to be produced in larger volumes. The technology spread, and evidence of steel making from then on becomes increasingly common – 650 BC in Sparta, 400 BC in India and China, 4th century BC in Iberia, and so on. Advances in metallurgy sprung up here and there through trial and error.
The big challenge holding back steel production was the inability to achieve high enough temperatures to actually fully melt the iron. Chinese historians give a date of 513 BC to when Chinese metallurgists first were able to fully melt iron and pour / cast it. This resulted in rapid Chinese progress in cast iron technologies, but the rest of the world was slow to catch on. Around 200 BC the Han people in China created higher quality steel by combining wrought and cast iron, and by 100 AD their production of carbon-intermediate steel was routine. The Chinese were probably the first to use puddling to remove carbon via oxidisation, possibly invented blast furnaces (Figure 3), and in addition to other methods used water wheels to power the bellows which forced air into their furnaces. The Haya people, who lived in East Africa on the SW shores of Lake Victoria (now part of Tanzania), were achieving temperatures of 1,800 °C around 2,000 years ago to produce a high quality carbon steel. In Sri Lanka high temperature blast furnaces were invented which relied on strong monsoon winds to force air into them.
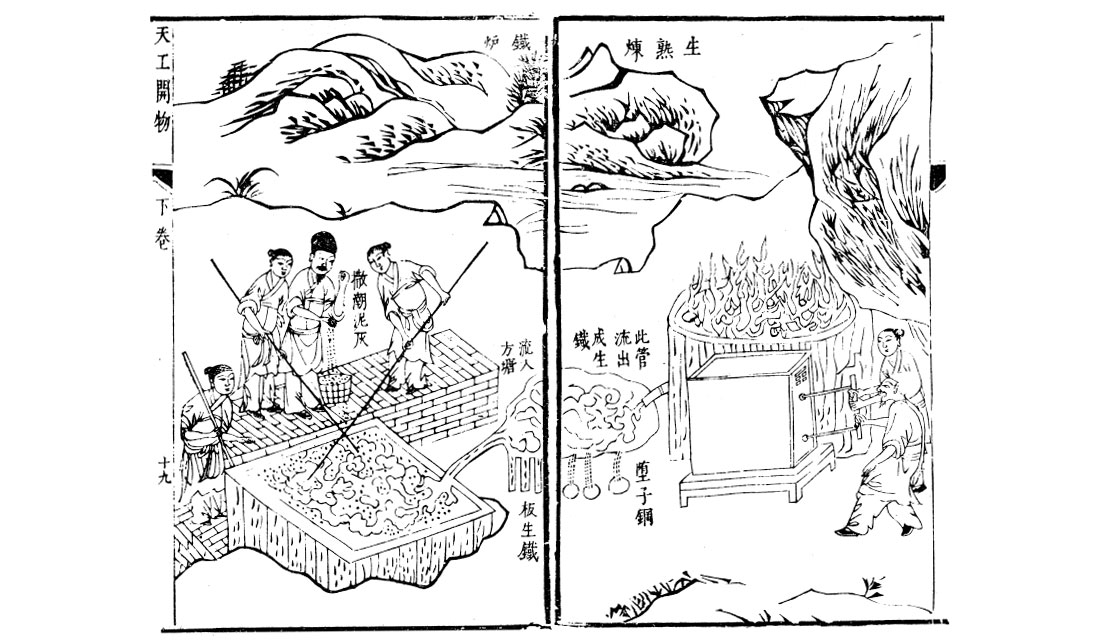
A big step forward was the switch from charcoal to coke as the fuel used during the creation of pig iron. Coke had been used by the Chinese as early as the 4th century AD, but Abraham Darby’s development in 1709 of a coke-fired blast furnace is often identified as the start of the industrial revolution, as it freed iron and steel production from a reliance on wood. Coke is usually formed from abundantly available bituminous coal with little ash and sulfur, and its purity and high carbon content make it the perfect fuel for blast furnaces producing pig iron.
Steel making methods improved in fits and starts over the centuries, but it really remained difficult and expensive to manufacture, and iron was the dominant metal until well into the 1800’s. Up to this point steel was produced using a method termed the cementation process. Alternating layers of iron bars and charcoal powder were racked in furnaces and heated over several days. The iron gradually absorbed the carbon from the charcoal. The carbon rich bars were then broken up and heated once more with charcoal powder, in an effort to more evenly distribute the carbon within the iron. The result was known as blister steel, and it was worked under forge hammers to give it a more even consistency. This method evolved into the crucible method, with the added step of melting the blister steel along with a flux (a chemical cleaning / purifying agent) to better remove impurities. This crucible steel was even higher quality, but expensive, and it was still very difficult to accurately control the percentage of carbon content.
In 1856 the invention of the Bessemer process marked the start of modern mass-production steel making. Sir Henry Bessemer’s idea was to force air through molten pig iron; the carbon (and impurities such as Si and Mn) within the liquid metal easily bonds with the oxygen at these temperatures, and the resulting gas and slag oxides are removed to create high quality steel. It should be noted that this concept of forcing air through molten iron to produce steel had been used outside of England and Europe for hundreds of years, but never before at an industrial level. So the big step forward was actually Bessemer’s converter (Figure 4), a large (volume of 5 to 30 tonnes of steel) tippable vessel with either a clay or dolomite lining, and nozzles called tuyères near the bottom through which the compressed air is blown. In the old days the colour of the flames escaping the top of the vessel gave a visual indication to the steel maker of the amount of carbon left in the steel. Nowadays automatic photoelectric methods are used to do this job, resulting in extremely accurate carbon contents.
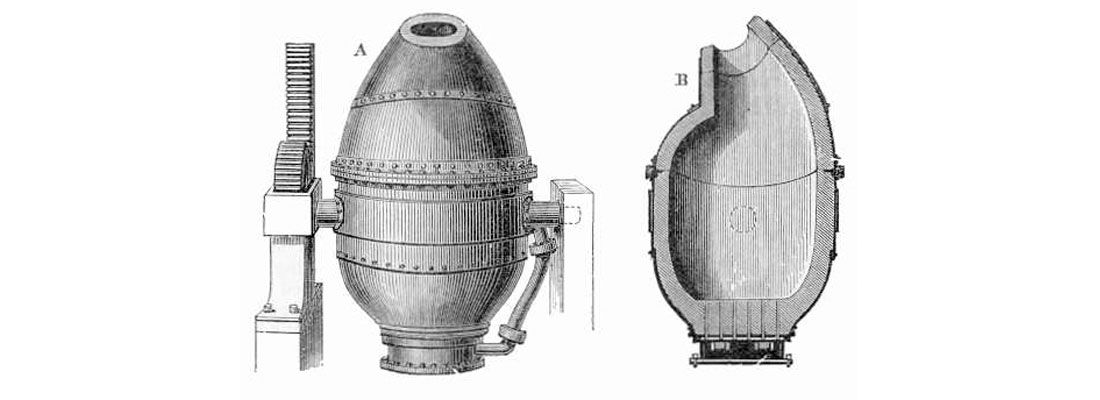
Two main further improvements to the Bessemer method followed. Early Bessemer steel was actually too low in carbon (and hence soft) and too rich in oxygen. The addition of an Fe-C-Mn compound, spiegeleisen (or spiegel), solved this, with the manganese bonding with the excess oxygen to form manganese oxide, and the carbon being absorbed into the steel and pushing the Fe-C balance to the desired level. Another major shortcoming of the process was that it did not remove phosphorus, an undesirable impurity. In the early years the workaround was that only phosphorus- poor iron ores were used, mainly from Sweden and Wales, but their rarity added cost. In 1876 Sidney Gilchrist Thomas discovered that if limestone is added to the molten pig iron, the calcium bonds with the phosphorus and floats to the surface, where it can be skimmed off. With these issues solved, steel production soared and prices plummeted. The resulting boom in cheap steel drove the expansion of the railway industry worldwide, which up until then had to choose between expensive steel rails, or soft iron ones which needed to be replaced frequently – every six to eight weeks on corners in some cases!
A last historical piece needs to be covered before moving on to current steel production methods. An alternative to the Bessemer method, the open-hearth method, was developed in Germany by Karl Wilhelm Siemens in the 1860’s, and it eventually displaced the Bessemer process. Instead of forming the steel in closed vessels, the iron was melted in broad, shallow open pits. Gas (first coal, then natural) was used as the heat source, and the exhaust from its combustion was used to preheat the air feeding the combustion; this made extremely high temperatures possible, despite the openness of the furnaces. High carbon pig iron and low carbon wrought iron were combined in proportions designed to achieve the desired percentage of carbon, and because the heating was done over a longer period than the Bessemer method’s ~ 30 minutes, much finer tuning of this critical aspect was possible, and the larger furnaces made production of much higher volumes of steel possible. The open-hearth method dominated steel production until the 1960’s, when the basic oxygen steel (BOS) and electric arc furnace methods (EAF) ushered in the modern era of steel making.
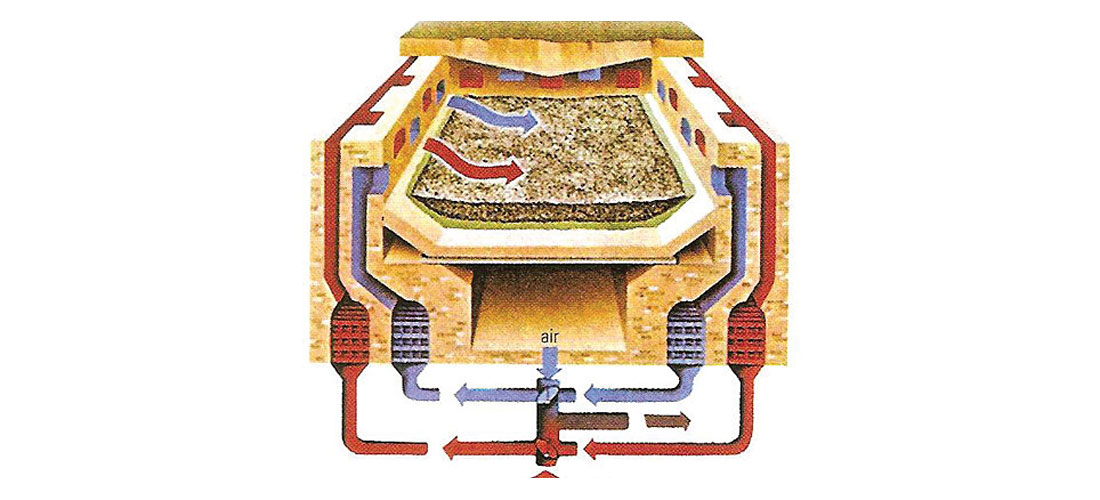
Modern Steel Production
Steel today is produced via two main methods – the LD converter basic oxygen process (BOS), and methods using the electric arc furnace (EAF).
LD Convertor / BOS
This method uses an LD converter (named after the towns Linz and Donawitz in Austria), essentially a variation of the Bessemer method which blows pure oxygen instead of air through the molten pig iron. Modern LD converters are huge, taking in up to 350 tons of pig iron in one batch, and turning it into low carbon steel in approximately 40 minutes. Most high volume steel mills use this method, and it produces approximately 70% of the world’s steel.
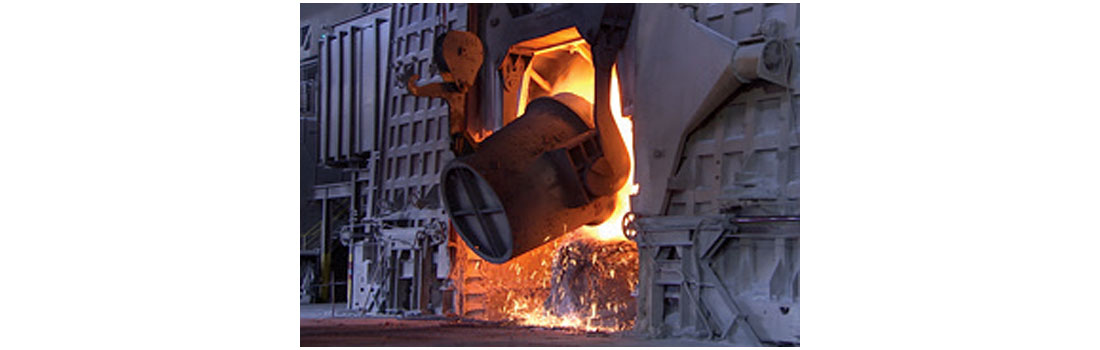
A summary of the main steps in BOS production will highlight the incorporation of the many advances in steel making over the centuries.
- Iron ore pellets are melted in a blast furnace, along with coke and limestone, to produce molten pig iron rich in carbon. This is then poured into a pretreatment ladle.
- The pig iron is desulfurized, desiliconized, and dephosphorized through the addition of reagents – powdered magnesium, iron oxide and lime respectively. The purer iron is then poured into the main furnace.
- The filling of the furnace is called charging, and is usually done with 4/5 molten pig iron, and 1/5 scrap iron, but the ratio depends on the desired balance of constituent elements C, Si, P, and S.
- A water-cooled lance injects pure oxygen into the molten pig iron at an extremely high velocity, and it immediately combusts when it comes into contact with the carbon, to form carbon monoxide and carbon dioxide gas; other unwanted chemicals tend to oxidize and are thus removed as well. This combustion raises the temperature to ~1700 °C which melts the scrap metal.
- A flux of either lime or dolomite is added depending on the proportions of sulfur and phosphorus, and this creates a slag containing most remaining impurities, a step called blowing. The chemistry of the molten blown steel is then tested.
- When the chemistry is correct, the furnace vessel is tipped into a different ladle, a step called tapping (Figure 6), where the desired secondary alloys are added and mixed.
- Once the molten alloy is a consistent mix, the finished steel is poured off and cooled, then worked into its raw finished form – sheets, bars, rods, etc.
Electric Arc Furnace (EAF)
With this method an extremely high voltage current is used to melt the raw feedstock, which is direct reduced iron (DRI) and/or scrap ferrous metal. Many mills preheat the feed materials with excess heat created during the smelting process, or with other methods. The size of EAF’s varies greatly, from 1 ton up to 400 tons, and thus the electricity required varies. However, it takes about 400 KWh to produce 1 ton of steel. Because of the high energy consumption, EAF mills are usually near cheap sources of electricity, and also tend to operate more at night and other times when there is excess electricity available from the grid.
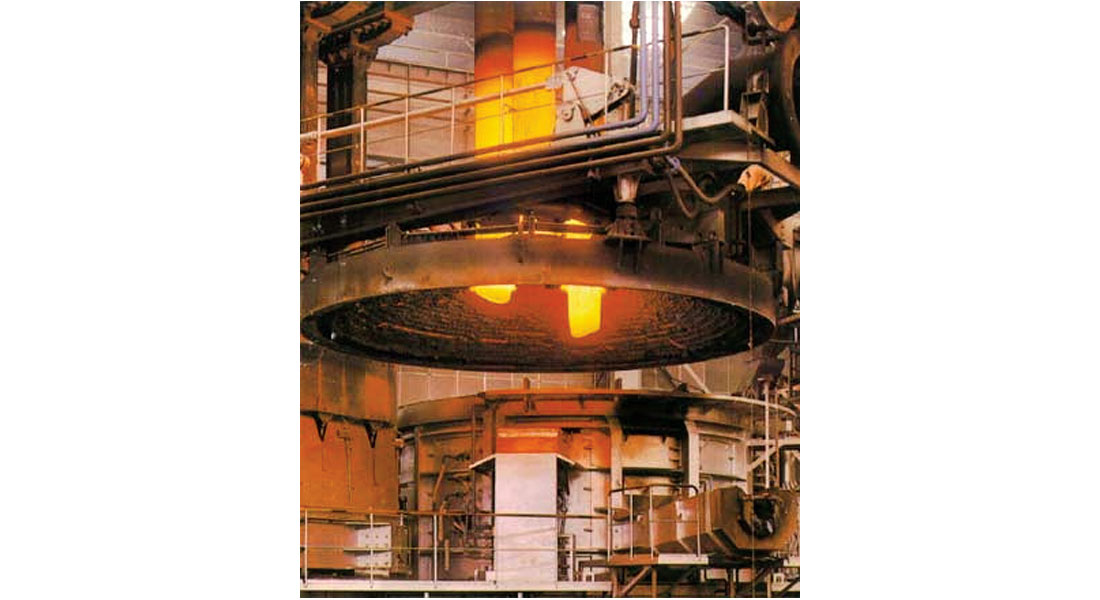
The input materials are layered in a scrap basket, optionally preheated, then dropped into the EAF, which has a roof which opens. The roof houses three electrodes (typically) which can be mechanically raised and lowered (Figure 7). The roof closes, power is directed to the electrodes, an arc forms, and the electrodes are lowered slowly and melt through the metal. Voltages start out low (relatively), and then are increased as the electrodes are repeatedly raised and lowered through the metal and the meltdown progresses. High pressure oxygen is injected into the vessel, and burners on the wall add to the heat. Similar to BOS methods, fluxes are added and slags are formed at the surface, which helps to protect the roof and contain the heat below. In conventional EAF’s, once the metal is totally molten then another bucket of scrap is added, and this is repeated until the vessel is full. However, leading edge single charge EAF’s are now being used.
Once the chemistry of the molten steel is correct, it is tapped out into a ladle through a taphole on the side. From this point on the process is similar to the BOS process, including the addition of alloys, quenching, etc. The entire process takes on the order of one hour.
Some of the advantages of EAF steelmaking have revitalised the steel industry and breathed life back into former rust belts such as in the northern US Great Lakes region – one success story is Nucor Steel, the largest steel producer in the USA, which almost exclusively uses EAF technology. Unlike BOS operations which find it hard to change production rates, EAF mills can start and stop production quickly, meaning they can adjust quickly in response to changes in market demand. EAF mills can also be very small, and located next to major markets; the term mini-mill is used to refer to small EAF operations. They also can make use of, in fact prefer, recycled scrap metals as their feed stock, thus tapping into the ever growing recycling trend, and reducing the amount of energy required since the feed stock is already closer to its finished composition. They are also better suited for the production of “long steel” such as rods, rails and tubes, although EAF technology has advanced to the stage that EAF mills can compete with BOS mills in the production of conventional flat steel.
References
Barron, A. R., & Smith, C. (2010, January 28). Crystal Structure. Retrieved September 16, 2013, from Connexions: http://cnx.org/content/m16927/latest/
Cambridge University Engineering Department. (2003). Teach Yourself Phase Diagrams – The Iron-Carbon Phase Diagram. Retrieved September 15, 2013, from University of Cambridge: http://www-g.eng.cam.ac.uk/mmg/teaching/typd/addenda/eutectoidreaction1.html
Dalian Xinlong International Trade Co., LTD. (2013). Graphite electrodes. Retrieved September 16, 2013, from Dalian Xinlong International Trade Co., LTD: http://www.dlxlcarbon.com/7.html
Darling, D. (Unknown). Open-hearth process. Retrieved September 16, 2013, from The Encyclopedia of Science: http://www.daviddarling.info/encyclopedia/O/open-hearth_ process.html
Dept. of Materials Science and Engineering. (Unknown). MSE 300 Materials Laboratory Procedures. Retrieved September 15, 2013, from University of Tennessee: http://web.utk.edu/~prack/MSE%20300/FeC.pdf
History World. (unknown). History of Metallurgy. Retrieved September 15, 2013, from History World: http://www.historyworld.net/wrldhis/PlainTextHistories.asp?groupid=1267&HistoryID=ab16>rack=pthc
Munawir, K. (2012, September 19). Diagram Fe-Fe3C. Retrieved September 15, 2013, from Belajar: http://sekolah007.blogspot.ca/2013/04/diagram-fe-fe3c.html
Spoerl, J. S. (Unknown). A Brief History of Iron and Steel Production. Retrieved September 15, 2013, from St. Anselm College: http://www.anselm.edu/homepage/dbanach/h-carnegie-steel.htm
United States Steel Corporation. (2012). Integrated Steel Making Process. Retrieved September 16, 2013, from United States Steel Corporation: http://www.ussteel.com/uss/portal/home/markets/construction
Wikimedia Foundation, Inc. (2005, December 4). Bessemer converter. Retrieved September 16, 2013, from Wikipedia: http://en.wikipedia.org/wiki/File:Bessemer_converter.jpg
Wikimedia Foundation, Inc. (2008, March 19). Chinese Puddle and Blast Furnace. Retrieved September 16, 2013, from Wikipedia: http://en.wikipedia.org/wiki/File:Chinese_Puddle_and_Blast_Furnace.jpg
Wikimedia Foundation, Inc. (various dates). Numerous Wikipedia pages including Steel, Steelmaking, Damascus steel, Wootz steel, etc.
Share This Column